Thursday, November 20, 2014
Ultra Fast Battery charger circuit
- Autoshut-off, is the ability of the charger to stop charging current to a NiCad battery if the capacity NiCad battery is fully charged.
- Polarity Protection, with the existence of this capability so if there are mounting the battery on the charger upside yan can be known.
- Constant output voltage
- Output currents enough to fill some NiCad batteries at once in parallel.
- Short Circuit Protection, with the existence of this protection circuit so if there is short-circuit caused by a battery and a charger circuit itself will not damage the other parts are not damaged.
- Series Ultra Fast Battery Chager for Nickel-Cadmium battery cells [NiCad]

AT89Sxx Base Board

Easy Downloader Circuit

Wednesday, November 19, 2014
144 MHz Simple RF Detector Circuit
When all the LEDs light, the (optional) UM66 sound / melody generator chip (IC1) also operates and provides an audible alarm. By changing the zener diode values of D2, D4, D6 and D8, the step size and duration of the instrument may change as needed. To operate in other bands of ham or PMR, simply change the network-L1 C1 resonance.
For example, a transceiver 5 watt handheld equipped with a telescoping half-wave antenna (G = 3.5 dBd), there is an ERP (Effective Radiated Power) of just 10 watts and an emf of more than 8 volts near the head. Inductor L1 consists of 2.5 turns of 20 SWG (approximately 1 mm in diameter) enameled copper wire. The inner diameter is approximately 7 mm and no core is used.
Trimmer capacitor C1 associates is adjusted for the greatest number of LEDs to light at a relatively low fieldstrength position for a 2 m transceiver 145 MHz transmission. The tester is powered by a 9 V battery and consumes about 15 mA when all LEDs are on. Must be enclosed in a metal box.
Preamplifier Microphone with 2 Transistor
Front of the microphone amplifier orpreamplifier microphone 2 transistor uses a system of dc negative feedback through R6which serves to provide stability strengthening. Level output signal from the microphonepreamplifier is controlled by potentiometer P1. Input signal that can be responded well by this microphone preamplifier is 0.2 - 200mV and 1V RMS output will result.

R1, R2, R3 100K 1/4W
R4 8K2 1/4W
R5 68R 1/4W
R6 6K8 1/4W
R7, R8 1K 1/4W
R9 150R 1/4W
C1 1uF 63V
C2, C3, C4 100uF 25V
C5 22uF 25V
Q1 BC560C
Q2 BC550C
TA8210AH Stereo Car Power Amplifier
Audio amplifier circuit can work at a minimum voltage 12-volt DC, if supplied under voltage 12-volt amplifier work will be less than the maximum. This amplifier output power up to 200W or 2 x 100W stereo with 8 ohm impedance.
R1 =1K
R2 =50K trim
R3 =1K
R4 =50K trim
R5 =680R
R6 =680R
R7 =150K
R8 =2R2
R9 =2R2
R10=2R2
R11=2R2
Capacitor
C1 =1uF
C2 =1uF
C3 =47uF
C4 =47uF
C5 =100n/400V
C6 =220uF
C7 =220uF
C8 =100n/400V
C9 =100n/400V
C10=100n/400V
Intregated Circuit
IC1=TA8210AH
Connector
X2-3=in R
X2-2=gnd
X2-1=in L
X1-1,X1-2=Out R
X1-3,X1-4=Out L
Tuesday, November 18, 2014
230Volt LED Circuit
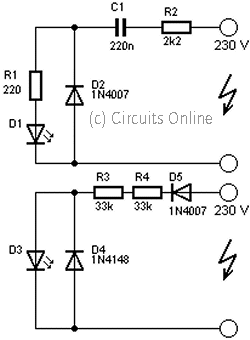
Loop Control Automatic Reversing Circuit Diagram
It is not the purpose of this folio to accommodate a abundant account of the ICs acclimated by this circuit. If you appetite added advice on this accountable amuse accredit to the Flip-Flop Made With A LM556 Timer Chip folio in the assorted circuits area of this armpit and additionally the Visible Light Photo Detector Circuits.
*The ambit uses the basal phototransistor detector ambit to faculty the position of a alternation that is abutting or is in the abandoning loop.
*Track polarity abandoning is not covered by this folio and will accept to be bent by the user.
Please Read Afore Using These Ambit Ideas
The explanations for the circuits on these pages cannot achievement to awning every bearings on every layout. For this acumen be able to do some experimenting to get the after-effects you want. This is abnormally accurate of circuits such as the "Across Track Infrared Detection" circuits and any added ambit that relies on added than absolute cyberbanking inputs, such as switches.
If you use any of these ambit ideas, ask your genitalia supplier for a archetype of the manufacturers abstracts bedding for any apparatus that you accept not acclimated before. These bedding accommodate a abundance of abstracts and ambit architecture advice that no cyberbanking or book commodity could access and will save time and conceivably accident to the apparatus themselves. These abstracts bedding can generally be begin on the web armpit of the accessory manufacturers.
Although the circuits are anatomic the pages are not meant to be abounding descriptions of anniversary ambit but rather as guides for adapting them for use by others. If you accept any questions or comments amuse accelerate them to the email abode on the Ambit Index page.
Video Amplifier Circuits
Interface LCD SED 1200 and Mikorokontroler AT89C2051
Monday, November 17, 2014
DC Motor Speed Control using PWM
Schmitt Trigger function that produces a square wave will become the sawtooth wave or integrator is also called common rail and the ramp compared to a reference voltage that can change a lot of stress. So the result is a PWM output.
PWMMotor Driver
![]() |
PWMMotor Driver |
GSM Cell Phone Jammer Circuit
This cellular buzz jammer isnt applicative for use in Europe, Center East, nor Asia. The GSM jammer ambit could block adaptable adaptable buzz signals which operates on GSM1900 band, additionally articular as DCS.
Timer 555 Schematic
Sunday, November 16, 2014
Kawasaki ZRX1200 Radiator Fan Circuit Diagram
To inspect and service the 2001 to 2006 Kawasaki ZRX1200 R/S radiator fan system, do the following:
* Remove fuel tank.
* Disconnect the 2 pin connector from radiator fan switch.
* Using an auxiliary wire, connect the radiator fan switch leads of the main harness side.
1. Radiator Fan
2. Radiator Fan Switch
3. Junction Box
4. Fan Fuse 10A
5. Main Fuse 30A
6. Battery 12V14Ah
Friday, November 14, 2014
INVERTER CIRCUIT 100 WATT
Block Diagram of Inverter

Main Components

Circuit Diagram

Explanation
- In the circuit diagram we can observe that 12V battery is connecter to the diode LED and also connected to the pin8 of the IC 4047 which is VCC or power supply pin and also to pin 4 and 5 which are astable and complement astable of the IC. Diode in the circuit will help not give any reverse current, LED will work as a indicator to the battery is working or not.
- IC CD4047 will work in the astable multivibrator mode. To work it in astable multivibrator mode we need an external capacitor which should be connected between the pin1 and pin3. Pin2 is connected by the resistor and a variable resistor to change the change the output frequency of the IC. Remaining pins are grounded .The pins 10 and 11 are connected to the gate of the mosfets IRF540. The pin 10 and 11 are Q and ~Q from these pins the output frequencies is generated with 50% duty cycle.
- The output frequency is connected to the mosfets through resistor which will help to prevent to the loading of the mosfets. The main AC current is generated by the two mosfets which will act as a two electronic switches. The battery current is made to flow upper half or positive half of the primary coil of transformer through Q1 this is done when the pin 10 becomes high and lower half or negative half is done by opposite current flow through the primary coil of transformer, this is done when pin 11 is high. By switching the two mosfets current is generated.
- This AC is given to the step up transformer of the secondary coil from this coil only we will get the increased AC voltage , this AC voltage is so high; from step up transformer we will get the max voltage. Zenor diode will help avoid the reverse current.
INTERFACING HEX KEYPAD TO 8051
Hex Keypad

Circuit Diagram

Program
About the Program
Important Points
- The 5V DC power supply must be well regulated and filtered.
- Column scanning is not the only method to identify the key press. You can use row scanning also. In row scanning a particular column is kept low (other columns are kept high) and the rows are tested for low using a suitable branching instruction. If a particular row is observed low then that means that the key connected between that row and the corresponding column (the column that is kept low) is been pressed. For example if column C1 is initially kept low and row R1 is observed low during scanning, that means key 1 is pressed.
- A membrane type hex keypad was used during the testing. Push button switch type and dome switch type will also work. I haven’t checked other types.
- The display used was a common cathode seven segment LED display with type number ELK5613A. This is just for information and any general purpose common cathode 7 segment LED display will work here.
Flashback VCR Cat Feeder from MAKE Volume 03
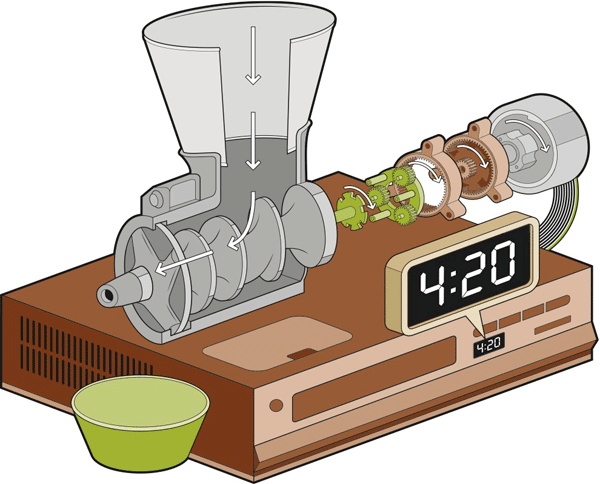
Check out the full project on Make: Projects, and also watch this clip of John Park demoing the feeder on Make: television:
Thursday, November 13, 2014
Radio Wave Alarm 4093 CMOS IC
This very simple alarm circuit is sure to have the police beating a path to your door - however, it has the added advantage of alerting you to their presence even before their footsteps fall on the doormat.

The alarm circuit transmits on MW (Medium Wave) (this is the small problem with the police). IC1a, together with a sensor (try a 20cm x 20cm sheet of tin foil) oscillates at just over 1MHz. This is modulated by an audio frequency (a continuous beep) produced by 4093 CMOS IC1b. When a hand or a foot approaches the sensor, the frequency of the transmitter (CMOS IC1a) drops appreciably.
Suppose now that the alarm circuit transmits at 1MHz. Suppose also that your radio is tuned to a frequency just below this. The 1MHz transmission will therefore not be heard by the radio. But bring a hand or a foot near to the sensor, and the transmitters frequency will drop, and a beep will be heard from the radio.
using LM741 Simple Electronic Bell Generator
Today I begs for to advise Simple Electronic Bell Generator , with Linear IC Op-Amp the number is highly popular be number LM741. By when press S1 as a result , will have sound signal bell come out and lead this signal goes to amplify talk at one time with power Amplifier Circuit The general. For Circuit the this friends must use Dual Power supply Source 9 Volt. Detail sizes are other friends has seen in the circuit , which not difficult yes.
8 Watt Audio Power Amplifier Schematic
Circuit diagram:
Parts:R1 = 47K
R2 = 2.2R/1W
R3 = 220R/1W
R4 = 2.2R/1W
C1 = 100nF-63V
C2 = 10uF-25V
C3 = 470uF-25V
C4 = 2000uF-25V
C5 = 100nF-63V
IC1 = LM383
SPKR = 4ohm/8W
Notes:
- IC1 must be installed on a heat sink.
- C1 is for filtering and to prevent oscillation and should not be omitted.
- The circuit can be built on a Vero Board, universal solder board or PC board, the PC board is preferred.
- The circuit draws about 880Ma at 12 V.
- By swapping the values of R2 and R3; you can turn this amplifier into a guitar amp with no preamp required.
- If you cant find 2000uF, then replace C4 with a 2200uF unit.
- If you add a 0.2uF capacitor in series with a 1 ohm resistor to the output you can prevent oscillation of the circuit under certain conditions.
Wednesday, November 12, 2014
45 Watt Class B Audio Power Amplifier
The idea sprang up from a letter published on Wireless World, December 1982, page 65 written by N. M. Allinson, then at the University of Keele, Staffordshire. In this letter, op-amp ICs were intended as drivers but, as supply voltages up to +/- 35V are required for an amplifier of about 50W, the use of an op-amp made of discrete-components was then considered and the choice proved rewarding.
The discrete-components op-amp is based on a Douglas Self design. Nevertheless, his circuit featured quite obviously a Class A output stage. As for proper operation of this amplifier a Class B output stage op-amp is required, the original circuit was modified accordingly. Using a mains transformer with a secondary winding rated at the common value of 25 + 25V (or 24 + 24V) and 100/120VA power, two amplifiers can be driven at 45W and 69W output power into 8 and 4 Ohms respectively, with very low distortion (less than 0.01% @ 1kHz and 20W into 8 Ohms).
This simple, straightforward but rugged circuit, though intended for any high quality audio application and, above all, to complete the recently started series of articles forming the Modular Preamplifier Control Center, is also well suited to make a very good Guitar or Bass amplifier. Enjoy!Circuit diagram:
R2_______________3.9K - 1/4W Resistor
R3,R6____________1K - 1/4W Resistors
R4_______________2.2K - 1/4W Resistor
R5______________15K - 1/4W Resistor
R7______________22K - 1/4W Resistor
R8_____________330R - 1/4W Resistor
R9,R10__________10R - 1/4W Resistors
R11,R12_________47R - 1/4W Resistors
R13_____________10R - 1W Resistor
C1_______________1µF - 63V Polyester Capacitor
C2_____________470pF - 63V Polystyrene or Ceramic Capacitor
C3______________47µF - 25V Electrolytic Capacitor
C4______________15pF - 63V Polystyrene or Ceramic Capacitor
C6_____________220nF - 100V Polyester Capacitor
C6_____________100nF - 63V Polyester Capacitor
D1,D2,D3,D4___1N4148 - 75V 150mA Diodes
Q1,Q2________BC560C - 45V 100mA Low noise High gain PNP Transistors
Q3,Q4________BC556 - 65V 100mA PNP Transistors
Q5___________BC546 - 65V 100mA NPN Transistor
Q6___________BD139 - 80V 1.5A NPN Transistor
Q7___________BD140 - 80V 1.5A PNP Transistor
Q8__________2N3055 - 60V 15A NPN Transistor
Q9__________MJ2955 - 60V 15A PNP Transistor
Power supply :

C1,C2_________4700µF - 50V Electrolytic Capacitors
C3,C4__________100nF - 63V Polyester Capacitors
D1_____________200V 8A Diode bridge
D2_____________5mm. Red LED
F1,F2__________4A Fuses with sockets
T1_____________230V or 115V Primary, 25+25V Secondary 120VA Mains transformer
PL1____________Male Mains plug
SW1____________SPST Mains switchComments:
- Output power in the 40 - 70W range
- Simple circuitry
- Easy to locate, low cost components
- Rugged performance
- No setup
- 2N3055 and MJ2955 transistors were listed for Q8 and Q9 as the preferred types, but many different output transistors can be used satisfactorily: TIP3055/TIP2955, TIP35/TIP36, MJ802/MJ4502 amongst others.
- Discrete op-amp output transistors Q6 and Q7 do not require any heatsink as their cases remain at ambient temperature. Power transistors Q8 and Q9 should be mounted on a black, finned heatsink as usual.
- 45 Watt RMS into 8 Ohms - 69W RMS into 4 Ohms
- 0.81V RMS input for 45W output
- 15Hz to 23KHz -0.2dB
- 1W 0.008% 20W 0.008% 45W 0.016%
- 1W 0.01% 20W 0.015% 45W 0.025%
indicator alarm for Water level circuit with explanation
This electronic circuit is a simple water level indicator alarm that is based on few transistors . The circuit is very simple and it has a very low current consumption , so you can use a 9 volts battery to powering this water level indicator alarm . This water level indicator alarm electronic circuit can be used even for rain alarm or short circuit alarm , a resistance with a value from 0 to about 1 M ohm will trigger it . The Q1 transistor acts as a switch which applies current to the unijunction relaxation oscillator Q2 . The signal frequency of the alarm circuit is give by the values and ratios of the C1 / R2 .
If you don’t have the transistors marked on the schematic diagram you can replace them almost with any similar types . As you can see in the schematic diagram , between probes is mounted a switch ( you can use a push-button) for testing the circuit , but it can be removed .
The speaker used in this project must have a impedance between 15 and 90 ohms .
LM317 based DC motor speed controller with circuit
A very simple DC motor speed controller circuit can be constructed using a LM317 voltage regulator integrated circuit . This DC motor speed controller can be used for speed control of mini drills or for other small DC motors . This motor controller circuit will provide a large output current . The maximum output current from the secondary turns of the transformer shout provide 1.5 times of the maximum DC output current . The output voltage and the speed ( rpm ) is set by the P2 variable resistor .
As soon as the current drawn exceeds a certain value , T2 will be switched on . This results in a base current for T3 so that R5 is in parallel with R6 . This automatically raise the output voltage to counter a threatened drop in rpm . The moment at which this action occurs is set by P1 .
Suzuki GSX400F’82 Signal Generator Circuit Diagram
The 1982 Suzuki GSX400F signal generator is mounted on the right hand side of the engine in the area commonly used for contact breaker point. It is comprised of a magnet embedded rotor attached to a mechanical advance mechanism and two pick-up coils, with iron plates at their bases, affixed to a plate. Each pick-up coil consists of a coil of wire and a yoke or coil and is mounted, 180 degree apart on the plate. As the rotor magnet is turned past the coils, AC current is produced and used for switching within the transistor unit. The transistor unit controls power to the ignition coils and causes the spark plugs to fire at the proper time.
Tuesday, November 11, 2014
Mains Powered White LED Lamp

The bridge rectifier turns the AC voltage into a DC voltage. LEDs can only operate from a DC voltage. They will even fail when the negative voltage is greater then 5 V. The electrolytic capacitor has a double function: it ensures that there is sufficient voltage to light the LEDs when the mains voltage is less than the forward voltage of the LEDs and it takes care of the inrush current peak that occurs when the mains is switched on. This current pulse could otherwise damage the LEDs. Then there is the 560-ohm resistor, it ensures that the current through the LED is more constant and therefore the light output is more uniform.
Source link:http://www.extremecircuits.net/2010/07/mains-powered-white-led-lamp.html
Saturday, November 8, 2014
Sounds From The Old West
S1 – bugle
S2 – neighing
S3 – sound of hooves
S4 – pistol shot
S5 – crack of a rifle
S6 – cannon fire
Circuit diagram:
Pan Pot
Circuit IC1 at the input is a buffer stage. It is arranged as an inverter to ensure that the phase of the input signal is identical to that of the output signal. The input impedance is set by R1 (10 kΩ). The output of the buffer is applied to stereo amplifiers IC2 and IC3. A special arrangement here is the positioning of P1, in conjunction with R3, R4, R8, and R9, in the feedback circuits of both amplifiers. This means that any adjustment of the potentiometer will have opposite effects in the amplifiers.
Series resistors R7 and R12 serve to ensure that the outputs can handle capacitive loads. Coupling capacitors C3, C6, and C9, may be omitted if an offset voltage of 20–30 mV is of no consequence in the relevant application. Capacitors C2, C5, and C8, ensure that the op amps remain stable even at unity gain. Capacitors C1, C4, and C7, minimize any r.f. interference, resulting in a usable bandwidth of 2.5 Hz to 200 kHz.
The performance of the circuit is of sufficiently high quality to allow the pot being incorporated in good-quality control panels. Total harmonic distortion plus noise (THD+N) at a frequency of 1 kHz and a bandwidth of 22 kHz is 0.0014%. Over the band 20 Hz to 20 kHz and a bandwidth of 80 dB, this figure is still only 0.0023%. The circuit needs a power supply of ±18 V, from which it draws a current of about 16 mA.
Simple Electronic Quiz Switch
Similarly, when any other switch (S2-S4) is pressed, the corresponding number gets displayed on seven segment displaying DIS1 and buzzer sounds. Switch S5 is used to reset the display exclusively. Switch S5 is a push to on switch. The circuit is powered by 9V battery. Assemble the circuit on a general purpose PCB and enclose it in a suitable case along with seven segment display and piezo buzzer. The assembled circuit can be kept near the host and the switches connected through the external can be assigned to the players.
12 V Glow Plug Converter
Friday, November 7, 2014
The Millipede
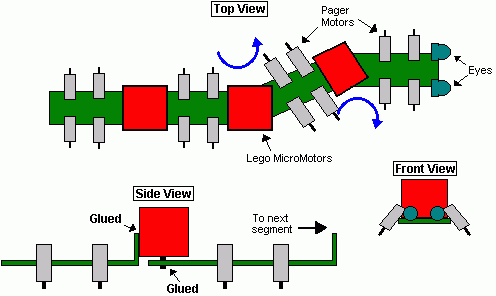
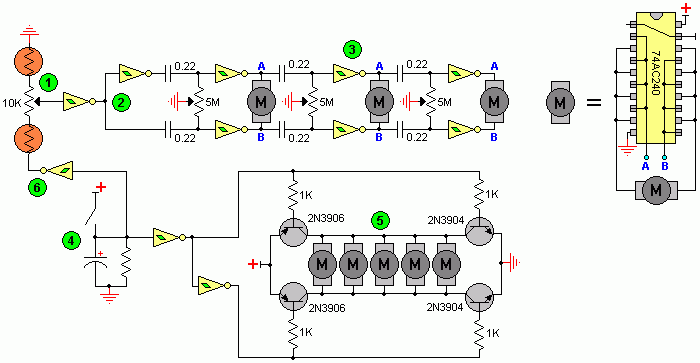
1 | This is the voltage divider. It divides voltage depending on which side is more iluminated, then, the schmitt changes the signal from a wave to a straight pulse. |
2 | The (usual) Nv only works when the input receives a HIGH, and that is the job of the schmitts. If the first schmitt outputs a HIGH the the lower strip of Nvs will work, the upper strip should stay calm because the second schmitt inverts the signal to a LOW. Thanks Math!!! |
3 | I can now be sure that there wont be 2 pulses on a same motor, and that when the first motor turns left (or right) the next one will also turn that same way, and the next and the next.... Only the first motor is affected by light, the others follow (in a wave pattern) the one before themselves. Since the millipede is moving forward while all this happens, a nice wave should appear when the bot has locked his path towards the light source. |
4 | This is the backup switch. When the bot bumps into something like... Hmm....anything, the cap is discharged trough the right schmitt. The (now LOW) output of the schmitt will reverse the PagerMotors, thus, reversing the whole bot. |
5 | This is the PagerMotors driver. I took the 4 transistor circuit design and modified it to be used with only one input signal. I know I wont be able to drive the 16 motors with 2N390X transistors, I used them in the schematic only because I need to find more powerful ones. Probably FETs? |
6 | As an extra (Yupeee), when the bot reverses it also makes the spinal column think that light is fully comming only from one direction. Because of this, when the millipede reverses, it also turns to one side all the body. |